安装现场拼接运输汽车规格963mm, 975mm,1138mm长度963、560、920mm厚度80mm固定钢钉
施工便利性设计
安装与拆卸:模板的结构设计要便于安装和拆卸,尽量采用简单、快捷的连接方式,减少施工难度和时间。
清理与维护:考虑模板的清理和维护需求,设置便于清理的结构和通道,如在模板上设置可开启的清理孔,方便清理内部杂物和残留混凝土。
经济性设计
成本控制:在满足工程质量和施工要求的前提下,综合考虑模板的材料成本、制作成本、运输成本和周转次数等因素,选择的设计方案。
周转利用:设计可重复使用的模板结构,提高模板的周转利用率,降低工程成本。对于一些周转次数要求高的项目,可采用通用性强、易修复的模板。
与混凝土的适应性
热膨胀系数匹配:模板材料的热膨胀系数应尽量与混凝土接近,以减少在温度变化时因膨胀或收缩差异过大而导致的混凝土开裂或模板变形等问题。
表面特性:模板表面应不会对混凝土的凝结和硬化产生不良影响,且能混凝土与模板之间有适当的粘结力,在脱模时既能混凝土表面质量,又不会出现粘模现象。
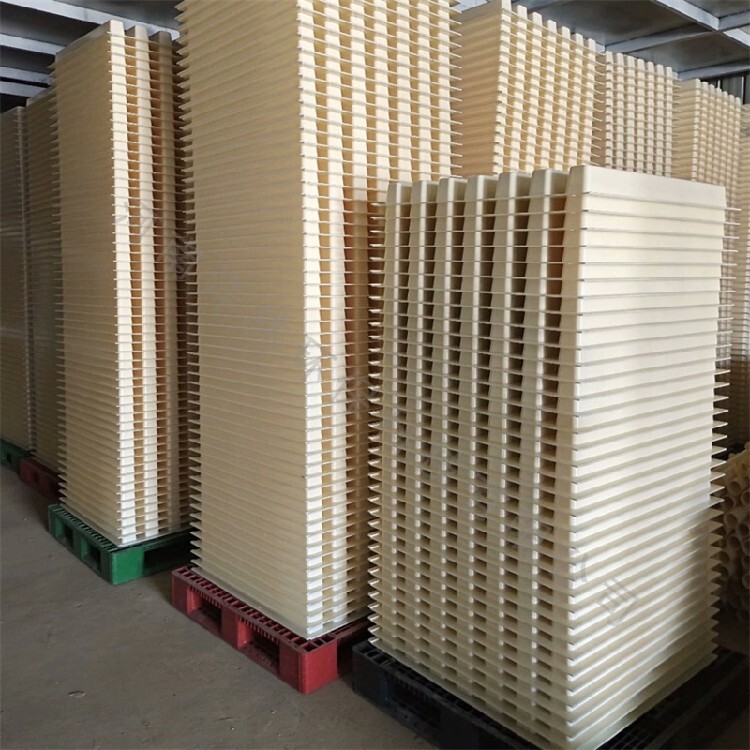
表面质量设计
平整度:模板表面应达到较高的平整度,以滤板表面光滑,一般要求表面平整度偏差控制在 ±1mm 以内,可通过对模板表面进行精加工处理来实现。
光洁度:模板表面要具有良好的光洁度,减少混凝土与模板之间的摩擦力,便于脱模,同时也能使滤板表面质量更好,可采用抛光、涂覆脱模剂等方式提高表面光洁度。
脱模设计
脱模角度:在模板设计时,应考虑设置合理的脱模角度,一般在 3°-5° 之间,以便于模板在混凝土凝固后顺利拆除,减少对滤板表面的损伤。
脱模装置:设置的脱模装置,如脱模孔、脱模拉杆等,方便施工人员进行脱模操作,提高脱模效率。
排水与透气设计
排水孔:在模板上设置适量的排水孔,孔径一般在 10mm-20mm 左右,以排除混凝土浇筑过程中产生的泌水,避免在滤板内部形成积水,影响滤板质量。
透气孔:合理布置透气孔,混凝土在浇筑过程中空气能够顺利排出,防止在滤板内部形成气泡,影响滤板的密实性和强度,透气孔的直径一般在 5mm-10mm 左右。
吊点设计
吊点位置:根据模板的尺寸和重量,合理确定吊点的位置和数量,确保模板在吊运过程中保持平衡,一般对于较大尺寸的模板,可设置 4 个或更多的吊点。
吊点强度:吊点处的结构要具有足够的强度和刚度,能够承受模板吊运过程中的荷载,防止吊点处出现撕裂、变形等问题。
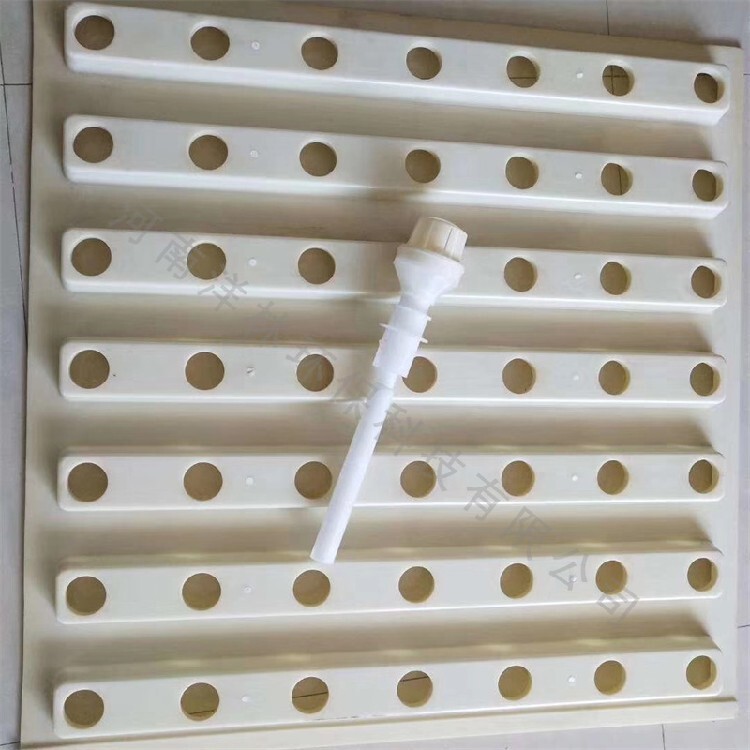
除了模板尺寸偏差外,影响滤池过滤精度的因素还有滤料特性、水流状态、设备运行维护情况以及原水水质等多个方面,具体如下:
滤料特性
滤料粒径:滤料粒径越小,过滤精度越高,但过小的粒径会导致水流阻力增大,过滤速度降低。例如,在处理饮用水时,采用较小粒径的石英砂滤料,能有效去除水中的细小颗粒和微生物,使出水水质更优。
滤料种类:不同种类的滤料对不同污染物的去除效果不同。如活性炭滤料对有机物有良好的吸附作用,而陶粒滤料则具有较大的比表面积和孔隙率,对氨氮等污染物的去除效果较好。
滤料层厚度:滤料层过薄,无法充分拦截和吸附污染物,过滤精度低;滤料层过厚,会增加水流阻力和运行成本。合适的滤料层厚度能过滤效果和运行经济性,一般快滤池的滤料层厚度在 0.7-1.2 米之间。